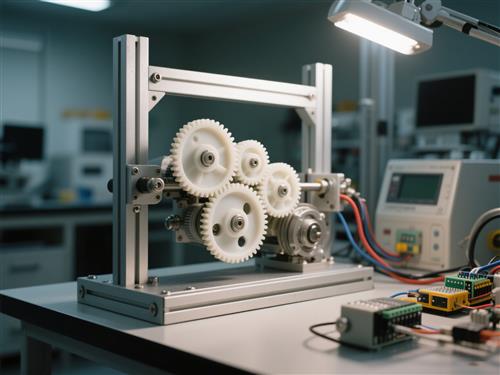
生產精密塑膠齒輪需從材料、工藝、設備到質量管控全流程嚴格把控,才能確保產品達到高精度與可靠性要求。以下從多個關鍵維度展開闡述。
精密塑膠齒輪生產的核心注意事項
在電子、醫(yī)療、半導體等對傳動精度要求嚴苛的領域,精密塑膠齒輪的生產不容絲毫馬虎。從原材料選擇到成品檢測,每個環(huán)節(jié)都需精準把控,才能確保齒輪達到微米級甚至納米級精度標準。以下從六大核心方面詳細解析生產精密塑膠齒輪的關鍵要點。
一、材料選擇:性能與精度的基石
精密塑膠齒輪的材料需兼顧高強度、低收縮率與良好的成型性。聚甲醛(POM)、尼龍(PA)、聚碳酸酯(PC)是常用材料。其中,玻纖增強尼龍因收縮率低至 0.8%,強度提升 40%,成為高精度齒輪的優(yōu)選;聚醚醚酮(PEEK)雖成本高昂,但在 260℃高溫下仍能保持尺寸穩(wěn)定,適用于航空航天等極端環(huán)境。材料的含水量、熔體流動速率等參數(shù)也需嚴格檢測,例如尼龍吸水后尺寸膨脹率可達 0.4%,必須提前進行干燥處理,將含水率控制在 0.1% 以下。
二、模具設計:精度傳遞的關鍵
模具精度直接決定齒輪質量。設計時需利用模流分析軟件(如 Moldflow)模擬熔體流動,優(yōu)化澆口位置與流道布局,減少熔接線與困氣。對于模數(shù)小于 0.5mm 的微齒輪,模具需采用慢走絲線切割或五軸聯(lián)動加工中心制造,精度控制在 ±0.005mm 以內。同時,模具表面粗糙度要達到 Ra≤0.2μm,并鍍硬鉻或涂覆 TiCN 涂層,增強耐磨性,確保 20 萬次注塑后齒形精度仍能達標。
三、注塑工藝:參數(shù)控制的藝術
注塑過程中,溫度、壓力、速度等參數(shù)需精確調控。料筒溫度波動超過 ±5℃,會導致熔體粘度變化,影響填充精度;保壓階段采用階梯式壓力控制(如先 90% 保壓 10 秒,再 60% 保壓 5 秒),可減少內部應力,避免齒輪翹曲。冷卻環(huán)節(jié)尤為關鍵,采用隨形冷卻水道或溫差循環(huán)系統(tǒng)(前模 80℃、后模 40℃),將模腔溫差控制在 5℃以內,能大幅縮短冷卻時間至 15-20 秒,同時保證尺寸穩(wěn)定性。
四、設備精度:穩(wěn)定生產的保障
精密注塑需配備高精度設備。伺服注塑機的重復定位精度要達到 ±0.01mm,確保每次注射量一致;齒輪測量中心(如 Klingelnberg P 系列)可實時檢測齒形誤差、齒距累積誤差等參數(shù),檢測精度達 0.1μm。此外,車間需保持恒溫恒濕(溫度 23±2℃,濕度 45±5%),避免環(huán)境因素對齒輪精度造成影響。
五、后處理工藝:精度提升的關鍵一步
注塑成型后的齒輪常需進行退火處理,將其置于 80-100℃環(huán)境中保溫 2-4 小時,消除內部殘余應力,防止尺寸后期變化。對于要求極高的齒輪,還可采用化學拋光或等離子體處理,進一步降低表面粗糙度,提升齒面光潔度,減少嚙合摩擦。
六、質量管控:全流程的嚴格把關
建立完善的質量管控體系是生產精密齒輪的核心。從原材料進廠的光譜分析、含水率檢測,到生產過程中的首件全檢、過程抽檢,再到成品的全尺寸檢測,均需嚴格執(zhí)行。采用 SPC(統(tǒng)計過程控制)對注塑參數(shù)進行實時監(jiān)控,一旦發(fā)現(xiàn)波動立即調整。同時,對不合格品進行失效分析,利用顯微鏡、CT 掃描等手段追溯問題根源,持續(xù)優(yōu)化生產工藝。
生產精密塑膠齒輪是一項系統(tǒng)工程,需在材料、模具、工藝、設備、后處理及質量管控等方面精益求精,才能制造出滿足高端應用需求的優(yōu)質產品。